Perfect in form
with global production capacities, innovative technologies as well as maximum flexibility and delivery service.
The whole spectrum of plastics processing – injection molding, foaming, extrusion blow molding
Being an experienced system supplier we provide you with a unique comprehensive package of thermoplastic processing: interlinked injection molding, extrusion blow molding, fully automated insert technologies and, if required, maximum purity in class 7 clean rooms. We see our strengths in the production of technically advanced large components. We produce flexibly, responsively and in accordance with our customers at more than twenty production sites worldwide.
- Fully interlinked global production solutions
- Of consistent, certified and reproducible quality
- Shot weights from 3g to 10kg
- Clamping forces from 250kN to 24,000kN
- Unique combination of extrusion blow molding, injection molding and clean room production
- Processing of all conventional thermoplastics
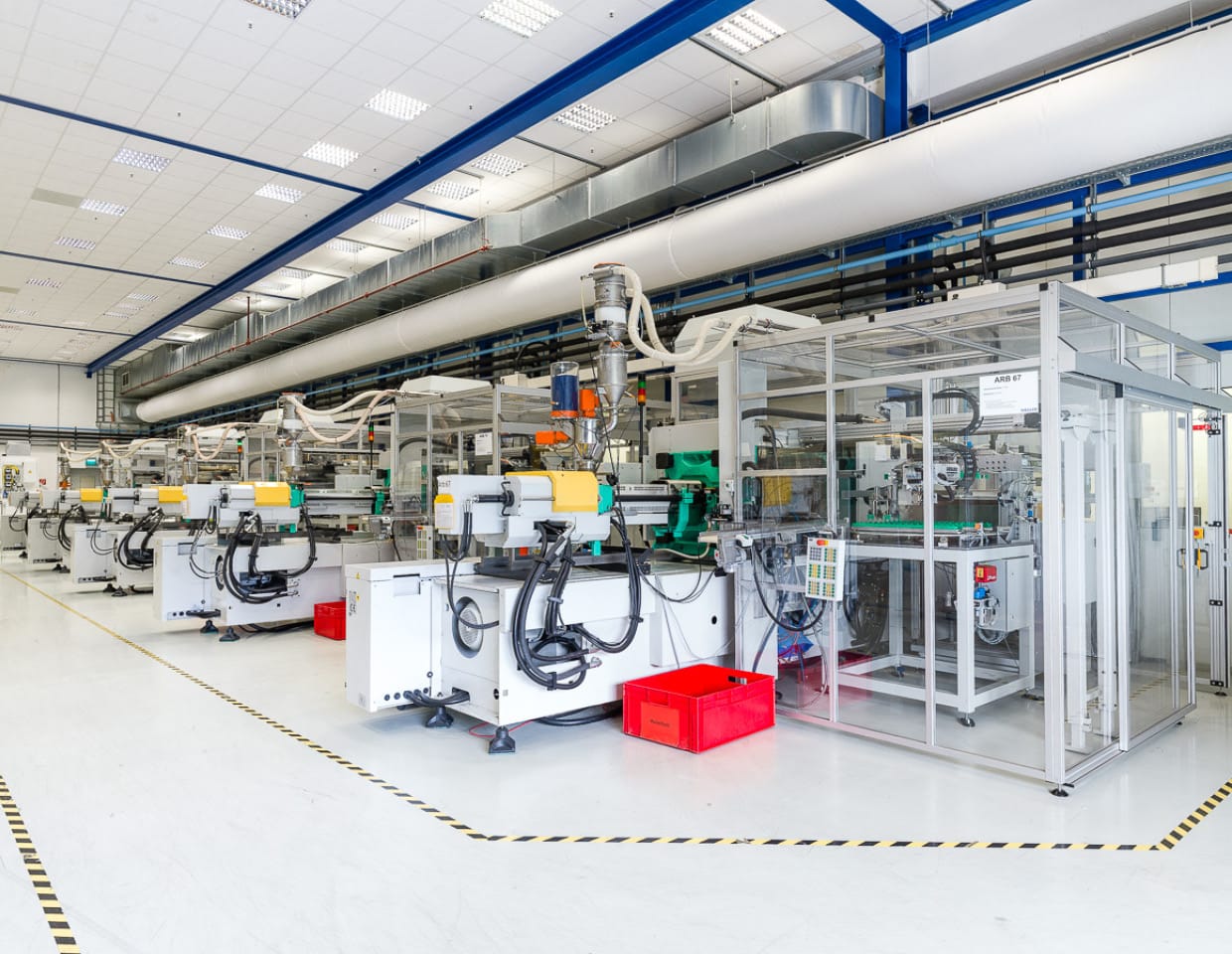
Injection molding.
With shot weights of up to 10kg and more than 500 group-owned injection molding machines we mold precise and state-of-the-art plastic articles. Sophisticated thermoplastics allow for an integration of functions and maximum freedom in design. Depending on our customers‘ specifications we use special technologies, such as assembly injection molding, multi-component injection molding, insert molding or cavity pressure. With our state-of-the-art machinery we exceed all our customers‘ expectations regarding delivery reliability and quality.
- Process improvement through mold sensor technology
- Multi-component injection molding
- Insert molding technology (horizontal and vertical)
- Assembly injection molding, stack- and tandem injection molding
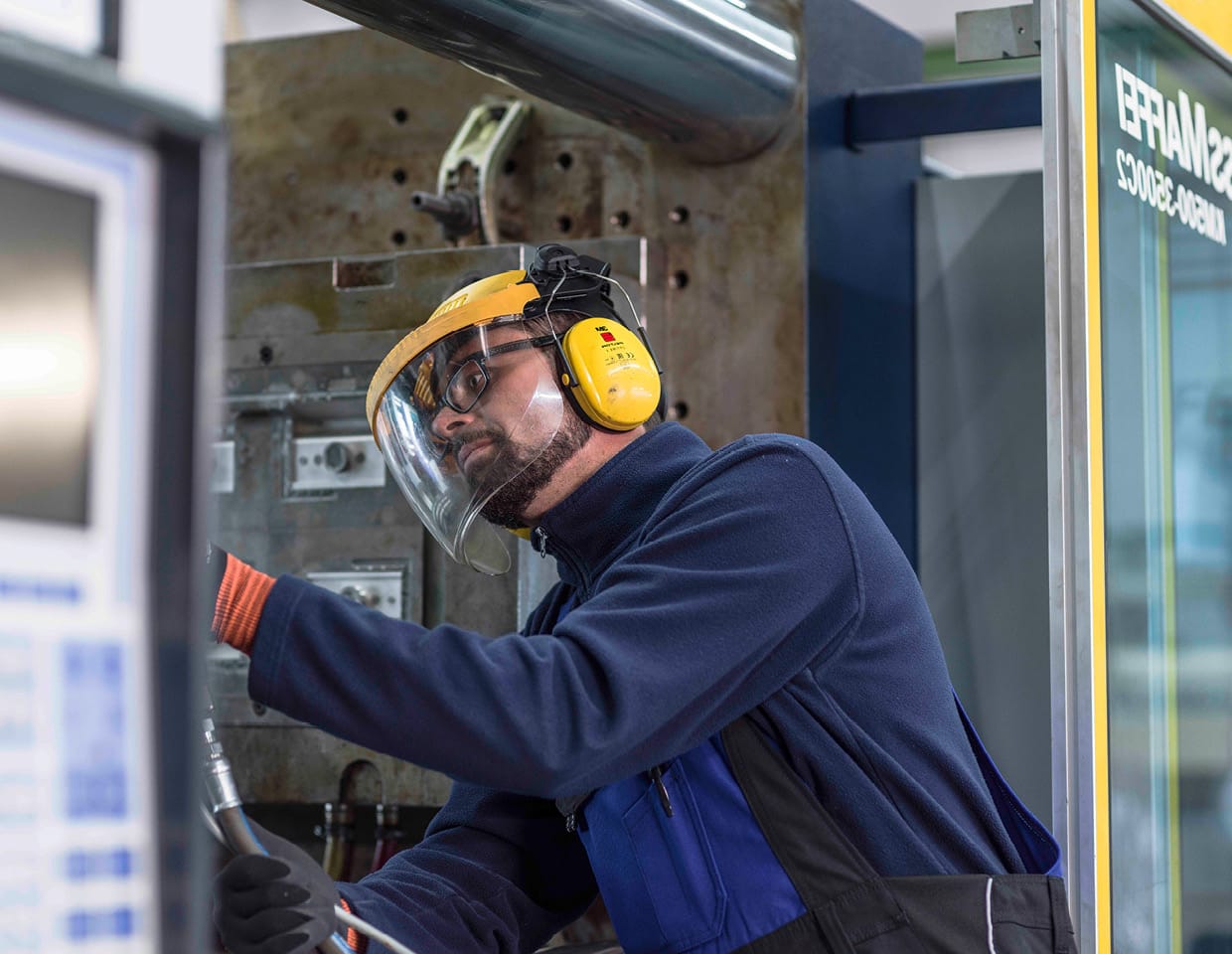
Thermoplastic foam injection molding.
Thanks to the thermoplastic foam injection molding procedure, such as physical foaming, articles can be manufactured more dimensionally stable, quicker, lighter and more cost-effectively. Along with the market leader MuCell® we also successfully apply the Cellmould® procedure to manufacture weight-reduced thermoplastic components in the automotive engineering and white goods sector. Depending on our customers‘ requirements and needs we flexibly expand our thermoplastic foam injection molding production capacities at the plants required.
- Chemical foaming
- Physical foaming (MuCell® and Cellmould®)
- Foaming of all conventional thermoplastics
- Several installations across Europe with clamping forces from 3,000kN to 16,000kN
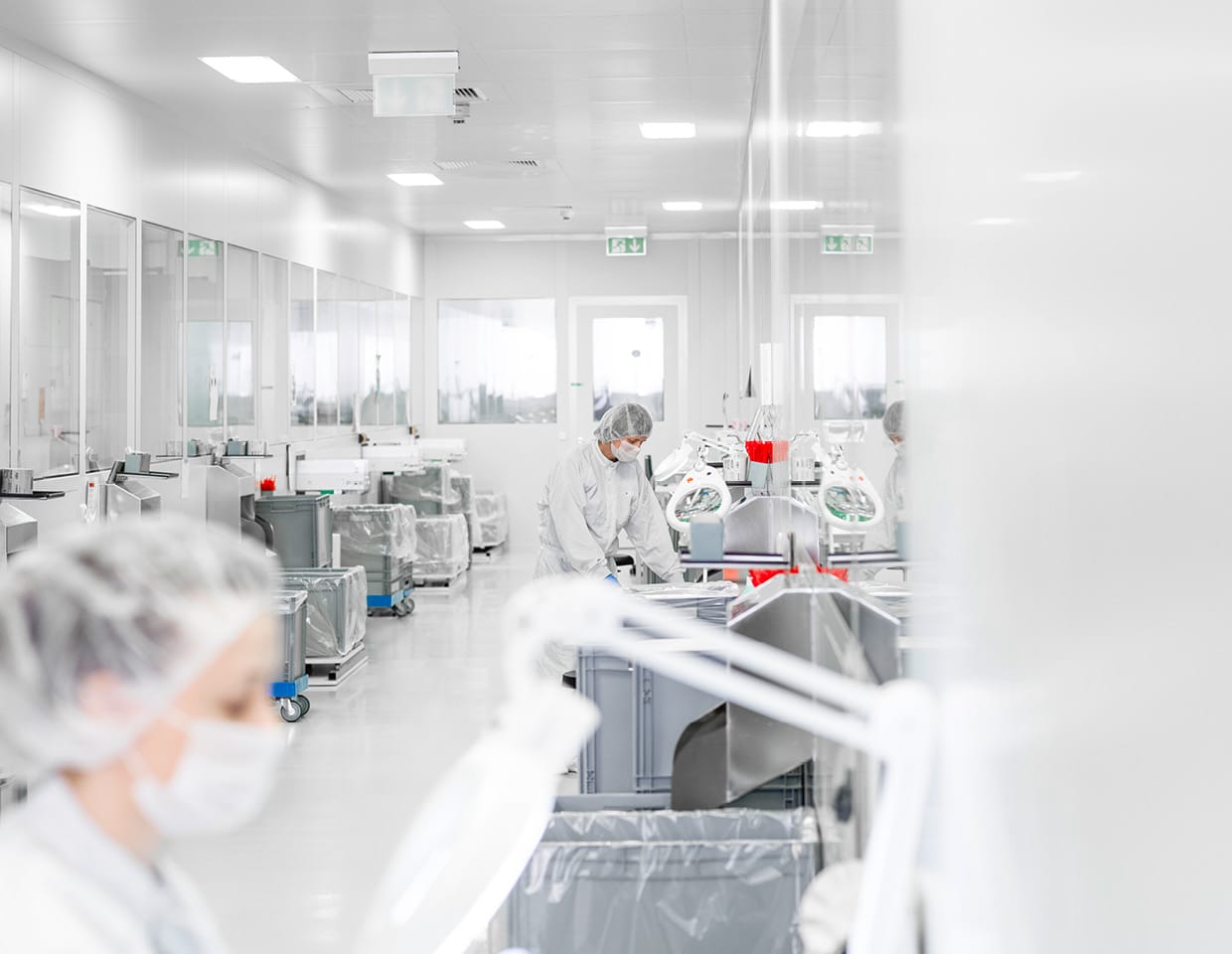
Clean room production.
When it comes to high article purity and dust-free molding processes, we produce in our certified ISO class 7 clean rooms under standardized and controlled conditions. Based on our hygiene guidelines according to DIN EN ISO 14644 and consistent process monitoring, we meet the requirements regarding particle concentration, air temperature, pressure and humidity. Our customers from the pharmaceutical and medical technology industries profit from maximum safety and efficiency, particularly in the application area of PCR or ATP hygiene monitoring.
- Hygiene monitoring
- Clean room ISO class 7, DIN EN ISO 14644-1
- Production with reduced ATP/RNA/DNA
- Production according to GMP standard
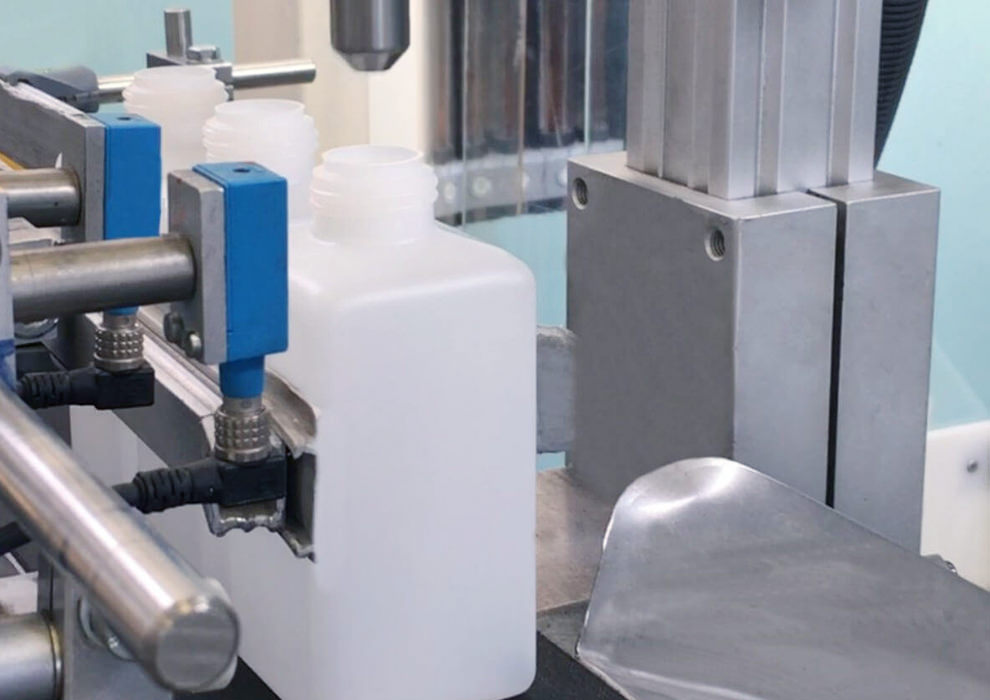
Extrusion blow molding.
Dimensionally stable bottles, tubes or technical hollow bottles are manufactured on state-of-the-art extrusion blow molding production lines. Being an expert in tempering, controlled molding of molten mass and accurate blowing of molded blanks we implement complex geometries and sophisticated functional components. We produce under the laminar flow clean room technique for pharmaceutical and medical applications.
- Number of cavities from 1+1 to 4+4
- Volume from 5ml to 6l
- Production under laminar flow
- Cleanpack packaging
- 100 % camera inspections and leak tests